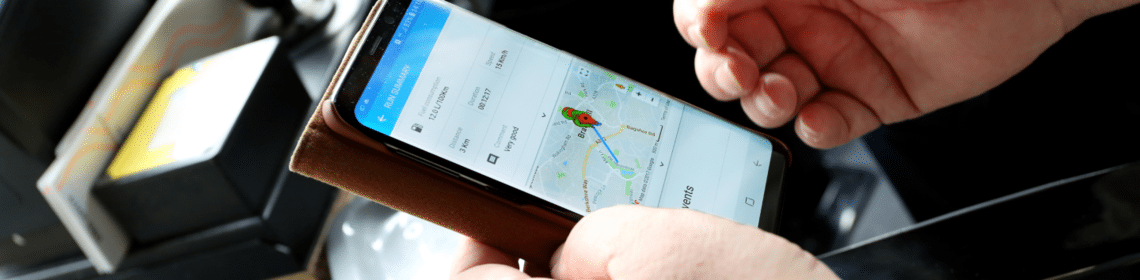
wave5 fleet efficiency header
Seeing, understanding, planning, and optimising transport activities, often in real time... Over the past decade, big data has gradually become a key ally for the owners of fleets of all sizes. Thanks to long-range connectivity, the status of trucks—transporters’ main profit centres—can be monitored non-stop to anticipate or even prevent breakdowns. How can data-based preventive and predictive maintenance tools and services from truck and tyre manufacturers make your fleet more efficient?
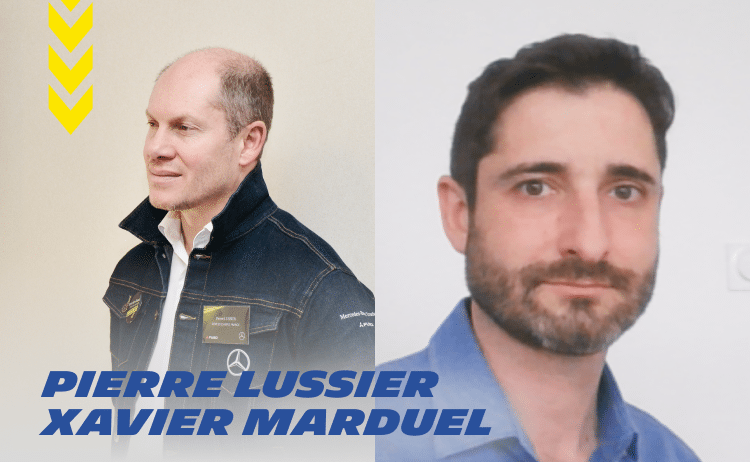
wave5 fleet efficiency img1
Pierre Lussier MERCEDES-BENZ TRUCKS FRANCE and Xavier Marduel Michelin Connected Mobility and Fleets expert.
Check out our special feature including: an interview with Pierre Lussier(1), head of connectivity at Mercedes-Benz Trucks France, a user story from Hervé Grosmaire(2), director of Les Transports Chaplain, and an explainer by Xavier Marduel(3), a Michelin Connected Mobility and Fleets expert.
DEFINITION : BIG DATA
Refers to the enormous volumes of digital data generated by a wide range of sources in our daily lives.
It is often defined by the 3 Vs: Volume, Velocity, and Variety.
When applied to vehicles, for example, data enables fleet managers to collect information that helps them make key decisions with a direct impact on costs and their company’s performance virtually immediately.
“Thanks to data, transporters have access to a continuous stream of targeted information on their fleets. And this is just the beginning!”
Pierre LUSSIER, Mercedes-Benz Trucks France
Pierre Lussier has been the Head of Connectivity at Mercedes-Benz Trucks France since 2013. He is responsible for marketing MB Trucks’ connected services to transporters. Pierre has been with Mercedes-Benz for over two decades in a variety of roles, including customer service positions in France, Germany, and the US.
Could you give us a brief overview of the history and the basic principle of MB Uptime?
Behind MB Uptime, there's a simple observation: a stopped truck is a truck that costs money. A vehicle is only profitable when it's moving! How could we, as a manufacturer, keep that essential equipment on the road longer? In other words, how could we limit the impact that breakdowns have on transportation businesses, or at least decrease downtime to an absolute minimum to reduce costs?
The project started in the early 2000s with the Fleetboard Services and Fleetboard Uptime services, which provided a snapshot of a vehicle at a point in time. The initial version of the program was launched with the Actros 4 in 2011. V1 was just raw data, with no alerts or algorithms. It only reported default codes. The current, more complete version dates from 2017.
Fully automated telediagnostics can now constantly monitor vehicle system statuses in real time. In just a few seconds, the data collected by a few hundred sensors on each truck is interpreted, critical statuses are identified, and actions are recommended via alerts in the customer interface, by phone, and by email to transporters and Mercedes-Benz certified workshops, all with the customer's consent.
We were actually the first truck manufacturer to develop a telematics system in the broad sense: a device with a number of associated services.
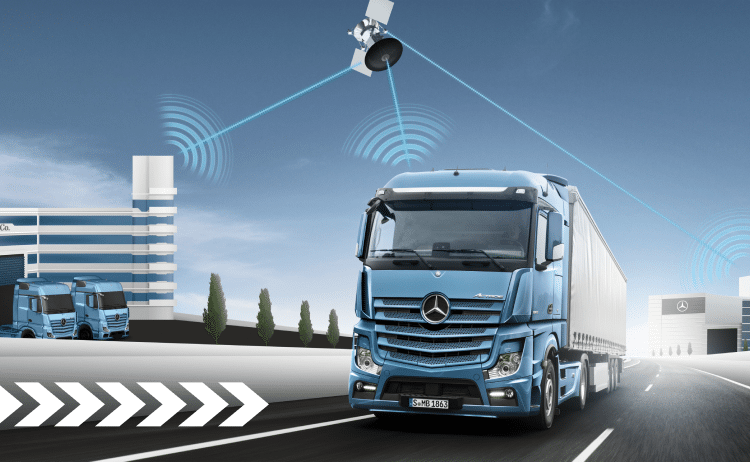
wave5 fleet efficiency img2
How does MB Uptime work?
It’s all based on smart connections. MB Uptime ushered in a new era of using data to serve transporters, with extensive analysis of the information that we collect and process in real time.With MB Uptime, fleet owners have access to 4 levels of information.
1/ Basic real-time information on their vehicles. The customer can view their fleet at any time.
2/ Real-time alert management on their vehicles. This is usually an orange dashboard light that comes on but does not require stopping the vehicle. The information is sent to the MB Uptime portal. The contact person sends the information to the driver, who can usually fix the problem independently and avoid a trip to the garage.
3/ Preventive maintenance and repair management, which corresponds to normal mileage-based vehicle maintenance. The Mercedes-Benz workshop receives an alert 3 or 4 days before the normal maintenance date. It can proactively contact the customer to schedule an appointment and plan for the work.
4/ Finally, we have the last level of information, which corresponds to preventive breakdown maintenance. It’s the most impressive, but also the least common—luckily!—with an alert 2 to 3 hours before the red light (which indicates major or severe breakdown) comes on. The predictive algorithms identify that the vehicle is going to suffer a breakdown that will bring it to a stop and organise a trip to the garage. The certified garage is notified so it can limit the impact of the breakdown on the transporter's business as much as possible, either by immediately ordering and replacing the worn part or parts involved or by finding a solution to get the merchandise to its destination on time.
Data collection offers a wide range of benefits for transporters, who enjoy access to continuous targeted information on their fleets. And that’s just the beginning!
“A stopped truck is a truck that costs money! Data analysis can prevent that.”
Pierre LUSSIER, Mercedes-Benz Trucks France
Could you share a real example of a time the system prevented or at least optimised downtime?
On Friday 22 March 2019 at 7:41 pm, MB Uptime detected the beginning of a leak on a high-pressure circuit on an Actros 1845 LS that was part of a fleet covered by a contract. At that point, no warning lights had come on and the driver probably hadn’t noticed anything out of the ordinary.
8 minutes later, at 7:49 pm, the platform contacted the customer to assess how urgent the issue was. The same day at 8:15 pm, the garage identified other repairs. It ordered all the necessary parts.
The truck finished its round and went into the workshop at 9:57 am on Monday 25 March. It was returned to the customer at 2:30 pm. The garage had replaced the injector, the fuel level sensor, and the air filter.
Remember that the service is operational 24/7, across Europe. Repairs don't stop at the border!
How does data help Mercedes-Benz develop the offers of the future?
Data is going to become a shared commodity. The biggest challenge is preparing our certified distributors and mechanics to handle data. The goal is to “make the data talk” and interpret it. Data processing should enable us to understand usage, identify needs, answer questions, and create new services to anticipate needs.
The first to achieve customer-oriented data processing, in other words ways of interpreting data that exactly meet identified customer needs, will be the winner.
When data is put into context and turned into alerts and recommendations, it is one of the keys to the mobility of the future. It is also an incredible tool for better customer relations management. We are going to achieve unrivalled quality of service. The possibilities are infinite. We will be able to identify recurring breakdowns and early warning signs so we can make changes right in our factories to improve reliability. We will also be able to offer virtually custom trucks that can address any fleet owner’s sustainable development and cost reduction challenges!
MB UPTIME IN FIGURES
· 1,500 rules are constantly monitored on each vehicle.
· Currently about 150 sensors on an Actros.
· One day of downtime represents an estimated revenue loss of €700 to €800.
· With MB Uptime, the average maintenance interval for an Actros goes from 120,000 km to 150,000 km, a 25% increase thanks to monitoring.
· Savings: up to €2,500 in maintenance costs alone over 5 years and 600,000 km (mainly due to the reduction in the number of oil and particle filter changes), before accounting for increased vehicle availability.
· Pricing: €22 per month (€254/year) and per vehicle without a maintenance contract (France and Europe).
€12 per month (€144/year) per vehicle as part of a full maintenance contract (France and Europe).
· MB Uptime penetration rate: 25% in France, 50% in Germany, and even higher rates in countries like Lithuania that rely on long-distance international transportation.
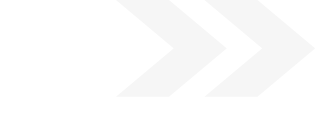
quotation right white
THE DIFFERENCE
Predictive and preventive maintenance: finding the right balance is key to avoid unnecessary interruptions!
Predictive Maintenance
Predictive maintenance is based on anticipation. It means monitoring trends that predict potential system failures in order to prevent them.
Preventive maintenance
As the old saying goes, “an ounce of prevention is worth a pound of cure.” Preventive maintenance means replacing, tuning up, or restoring an entire piece of equipment before a breakdown causes a chain reaction. In practical terms, that means performing vehicle maintenance to prevent a total breakdown.
USER STORY
“With MB Uptime, we can see the exact cost of a truck throughout its lifespan.”
Hervé GROSMAIRE, MB UPTIME customer
Hervé Grosmaire heads Les Transports Chaplain, an entity of the family-owned Chaplain group, which specialises in aggregate mining, earthworks, and concrete products. Founded in 1974 by Mac Chaplain, the Group is based in the Aube, in eastern France. The transport company currently has 60 vehicles (45 tractor trailers and 15 rigid-frame trucks). Two-thirds of those are Mercedes-Benzes and one-third are DAFs.
“We signed our first MB Uptime contract in 2017. Since then, all of our trucks have been under manufacturer maintenance contracts. Maintenance enables us to better control our costs. With MB Uptime, I can see the exact cost of a truck throughout its lifespan. That has enabled us to cut our costs by 3% per year since 2017!
The drivers had a little trouble with the new set-up at first. Until 2017, we had an in-house garage that handled maintenance. Now they have to go to the Mercedes-Benz garage in Troyes, about thirty minutes from our depot, for service. It was a habit that took time to develop, just like regularly checking their emails and the MB Uptime portal, but it has become completely automatic. I delegated the project to my operations manager.
In addition to fleet management and breakdown prevention, MB Uptime can be paired with the Fleetboard services to recover tachograph data and driver maps. That saves drivers a lot of time, since they don't have to go into the office anymore.
Looking ahead, I’m interested in using data to stay compliant.”
INNOVATIONS TO KEEP AN EYE ON : 2 technologies for easier tyre maintenance
An explainer with Xavier Marduel, a Michelin connected fleets and mobility expert.
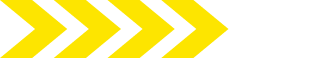
arrow highlight yellow
RFID Technology
> What?
RFID (Radio Frequency IDentification) or radio-identification, is a technology that can be used to save and recover data remotely using chips or tags with an electronic number that is impossible to forge. Michelin was one of the first tyre manufacturers to use this technology.
> How?
MICHELIN installs RFID tags in 100% of its Michelin truck tyres in Europe. The unique ID created by RFID technology improves traceability, efficiency, and safety throughout the tyre lifecycle.
> For whom?
All transport fleets, to optimise management of their maintenance operations by simplifying each operation with increasingly automated monitoring of tasks like stock entry, fitting, position verification, configuration of a new vehicle, rotation, turning on rims, retreading, and inventory.
> The benefit
The overall experience, particularly inventory quality, is improved. The risk of errors is reduced and the fleet operator saves time.
RFID technology eliminates issues with reading tyre serial numbers. In the specific case of retreading, RFID technology guarantees traceability and efficiency during the retreading process thanks to easier, more reliable casing identification and verification.
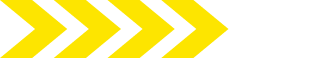
arrow highlight yellow
QuickScan: a proprietary Michelin technology
> What?
An automatic diagnostic technology for your tyres’ condition. It is quick and easy to install on-site. Installation takes just a half-day and does not require long site downtime or new electrical equipment.
> How?
As it drives over the scanner installed on the ground, the vehicle is identified by a small plaque attached to its body. The magnetic scanner measures tyre wear.
The data collected is then sent to a receiver located nearby, which sends it to a cloud where it is processed using algorithms developed by Michelin.
> For whom?
The system works for all heavy vehicles (tractors, trailers, and rigid-frame trucks), buses, and coaches, for all tyre brands, and in all weather, even snow, rain, and mud.
> The benefit
Michelin QuickScan analyses the data and then shares text and email alerts, depending on the offer selected, to notify the customer of any emergency services required. Summary reports that recommend actions to schedule are also sent out to help anticipate maintenance needs.
“Of course data processing is an asset for fleet owners. With the development of these new technologies, we are also seeing a “gamification” of work that improves tyre operators’ experience and adds an attractive element of innovation to their roles.”
Xavier Marduel, Michelin
(1)Interview with Pierre Lussier on 15 March 2022
(2)Interview with Hervé Grosmaire on 26 April 2022
(3)Interview with Xavier Marduel on 15 April 2022
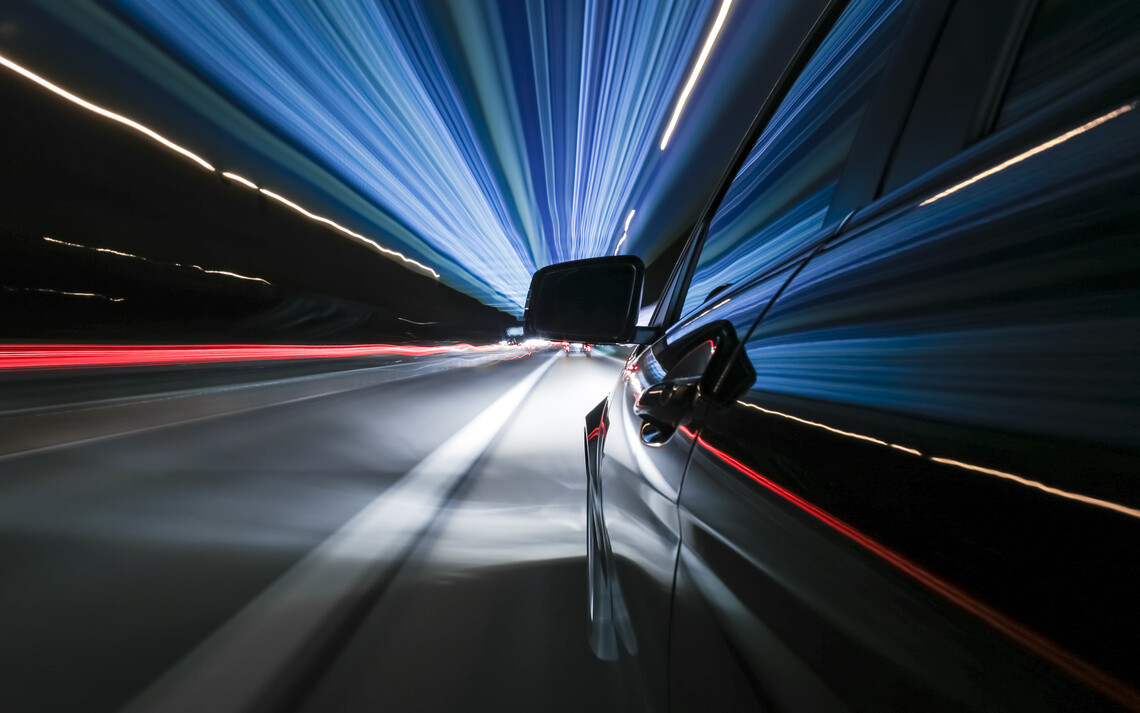
gettyimages 930571046
car going fast on a road by night